This is copied straight from my blog, please forgive the format as it doesn't quite read right as a forum post.
Enjoy!
With so many drivetrain options out there, it can be hard to choose. When planning any bike build for myself or customers I look at many factors;
•budget
•existing frame or new, dropout type and compatibility
•load capacity, terrain and gear ratio requirements
•temperature and operational environment
•serviceability, duty cycle and maintenance complexity
•spares, warranty support and local backup
• weight
For the Moonlander and the predominant terrain I'll be covering in Australia, the Nu Vinci N360 was a clear standout for me. I had several options on the short list, but what I really liked about the N360 was the seamless linear change between ratios. You see, the Nu Vinci N360 is a CVP transmission, so unlike other internal geared hubs (IGH) there is no definitive step between gear ratios - twist the shifter and the ratio smoothly changes. On the Nu Vinci site there are videos, graphs, diagrams - even a support bulletin board/forum - that explain the N360, but you really gotta ride it to understand it.
I'll mostly be riding on sand, so a key thing about riding on sand is momentum - any loss of momentum risks stalling - riding on soft sand can be likened to riding up a slight constant gradient. The N360 is able to be shifted under load, so momentum loss is minimised during shifts. The hub is sealed for life, with only the freehub section accessible for routine maintenance.
So, let's start. I wanted to minimise this:

The kit. For reference this kit was packed on 09-09-2010. This does have an influence on the external performance of the kit, as Nu Vinci have made several changes and improvements to a few components. I bought the kit through Southcott Cycles, the distributor here in Australia. There is also an axle quick release kit available, yet to order one of these.

The spokes didn't come with the kit, I would normally roll my own odd sized spokes with my trusty Hozan spoke roller, but in this case I got them cut down to suit my requirements. They are double butted Alpine spokes, with a 14g body/thread and 13g at the J bend. The 20T Surly sprocket is extra too, matched well to the 36T chainring to be within the 1.8:1 gear ratio restriction for the hub.
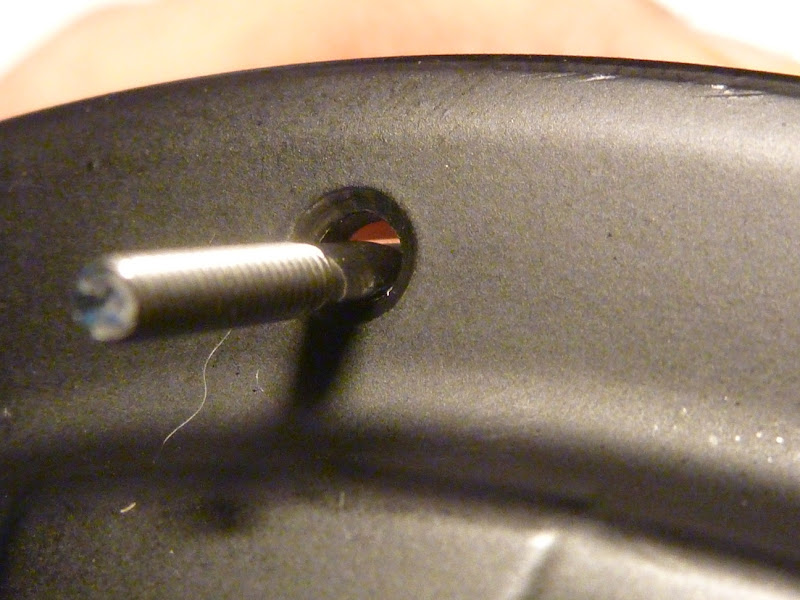
You can see how well the 13g head matches the hole size of the hub, providing a much firmer interface between hub and spoke.

One thing about the Moonlander, is the 28mm offset of the rear to clear the drivetrain. The Clown Shoe rims are drilled to allow for the offset, but the spoke cross pattern, length and dish must respect the 28mm offset. Spacer tools are available to achieve the correct dish, which I'll show as required during the build process.

After backing off the spoke tension a few turns, the nips are spun out.
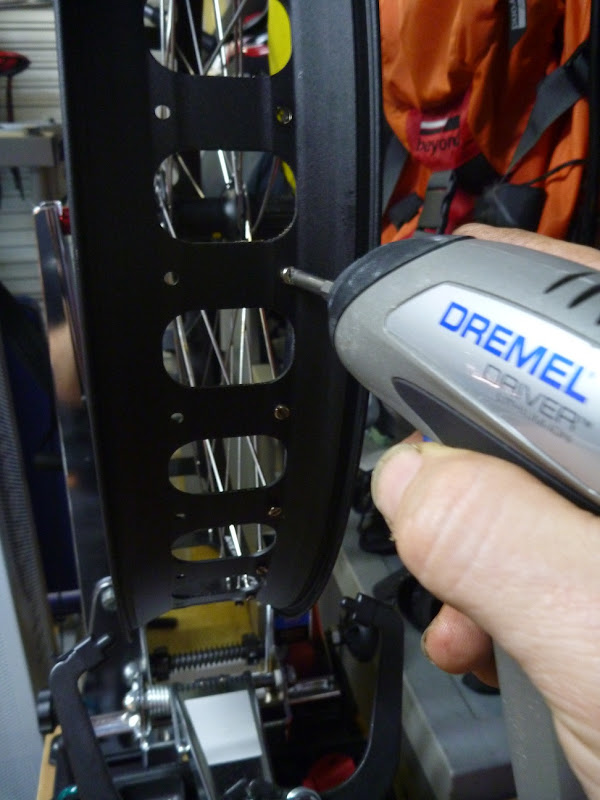
Then you should end up with a cool spiders web like this:
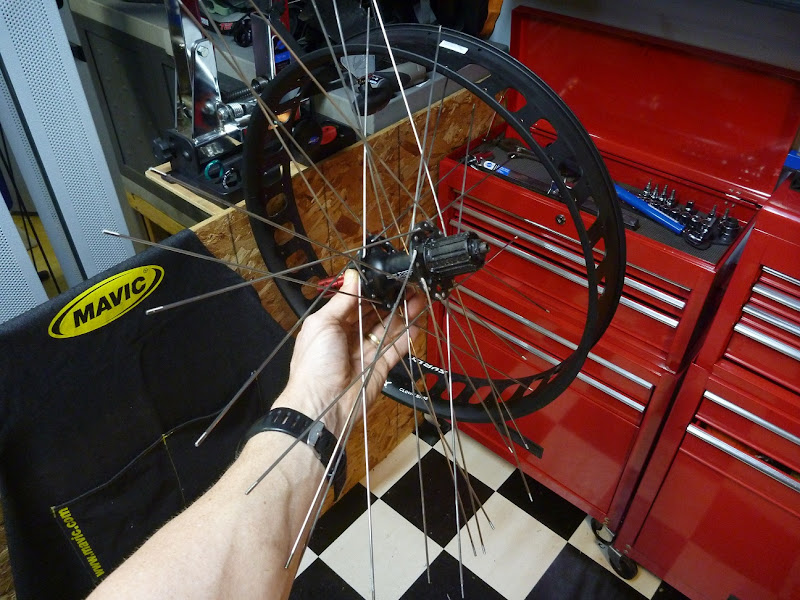
I wanted to prep the hub prior to installation, plus I wanted to see the innards of the freehub. I noticed there was a groove on the inside of the plastic cover on the right, but no o-ring in place. There was potential for contamination ingress at this point, so I sourced an o-ring from the spares dept, lubed the freehub pawls and needle roller bearings with some low viscosity freehub specific grease and reinstalled the cover and freehub body.


You can see here the slight gap between the plastic cover and the hub body - this is another point of entry for water, sand and general contamination.

Easy fix with a large o-ring to cover the gap. Should keep out a fair bit of debris, easy to remove/re-install when cleaning/servicing.

Two cross pattern is the recommended option, this gives a reasonable exit angle from the rim for the spoke. I have several special processes for my handbuilt wheels, the details of which are a close family secret, so we'll skip straight to the fully built wheel.
Due to the offset and dish of the wheel, I couldn't get the wheel in my Park Tool truing stand with the Moonlander dish tool, so I had to use the Pugsley 17.5mm offset tool in the stand, then swap to the 28mm tool for correct dish.

Spoke tension is quad checked during the build. No guesswork with tension.

Dishing the wheel.

I'm very specific with my spoke lengths. I like the end of the spoke to finish right at the end of the nipple, this maximises the strength of the nipple, regardless of nipple material. I've gone with regular brass to minimise corrosion. Any high spokes get trimmed with the Dremel. A quick weigh-in of the complete wheel with tube and tyre came in at 6.1kg. Not a light package, but weight was not really a high priority for this build.


The instructions are very well laid out and descriptive. My old mate Calvin from Park Tool also has a detailed installation writeup for the N360 on his blog, 'Calvins Corner'

The gear change interface is easy to set up, plenty of grease during assembly to keep contamination and corrosion away.

The shifting is effected by a two cable system, cable diameter is 1.1mm so SRAM outer casing was used, as well as genuine cable specific lube. Super sliiiiiiick.

Cable ends that clip into the shift interface on the hub:
The chain rubbed on the cable end as well as the shift interface, a quick flip of the sprocket rectified the chainline.


Much simpler cockpit, just the one twisty:

Much simpler drivetrain, no derailleurs or auxilliary chain devices:

End result is a much simpler bike externally, both visually and mechanically.

At the time of writing this, I have only ridden my N360 equipped Moonlander a handful of times on the street, in a week or so I will have solid data on how it performs, with a weekend riding on Moreton Island. We recently spent a week on the island with the original 2x9 drivetrain and saw how the sand affected the drivetrain, will be riding some of the same tracks fully loaded. Living the dream!